Post by Admin on Mar 12, 2016 22:34:00 GMT
CEHISA Pro Concept
DaltonsWadkin
The CEHISA Pro Concept is a hot melt automatic through-feed edgebander suitable for melamine, PVC, ABS, PP and veneer edging up to a thickness of 3mm and solid edging up to 8mm. An intuitive 5.6″ or 10″ touch screen control gives the operator quick access for monitoring all machine functions – start/ stop, program editing, parameters check and editing, alarm diagnostics etc all in real time.
Panels are fed through the machine with an industrial chain-track system running on ground steel guides. Non-marking traction pads ensure a positive feed without damaging the panel surface while the synchronised top pressure beam with two sets of rollers keeps the panel secured against the track.
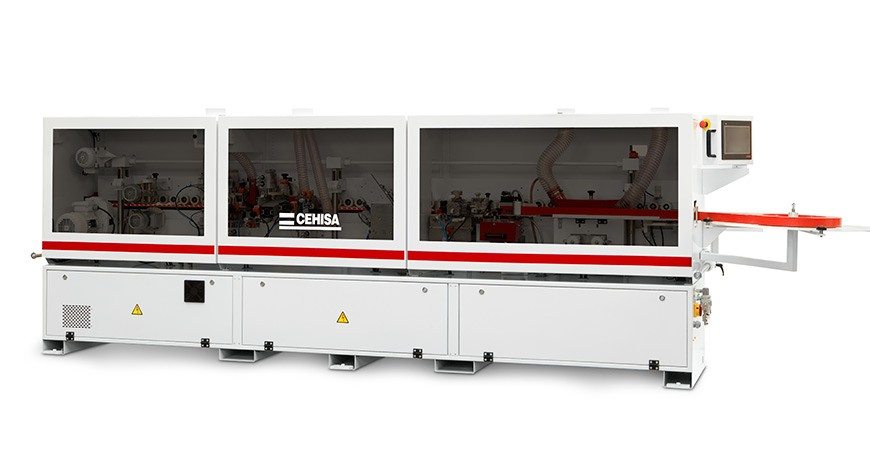
As standard the eight models within the PRO Concept range all include the following;
Feeding unit
roll tray for edging
feed up to 8mm thick solid edging manually
precision timed automatic edging feed minimising wastage
pneumatic cut-off guillotine
optional automatic magazine feeder for solid edging
Glue application unit (M-2NS)
new design with improved thermodynamics for quicker heating
quick change system for swapping the unit over in less than 60 seconds
full TEFLON coating
molten glue injected at the upper and lower points of the application roller where inbuilt heating elements maintain optimum application temperature
automatic temperature control by electronic thermostat to prevent scorching of glue while machine idle
1.5 kg glue tank capacity of solid aluminium casting machine to a smooth finish to allow uninterrupted glue flow
optional DUMELT system for use of both EVA and PUR adhesives
Pressure rollers
three rollers exert pressure to the edging against the panel to achieve adhesion
first roller is driven, the second and third are idle
the first roller is cylindrical and the second two conical in opposing positive and negative directions
SIKO digital readout for unit adjustment to 3mm edge/ 8mm solid edge
End trimming units (V-7)
two independent high frequency sawing units running at 12,000 rpm trim the ends of the edging flush to the panel
precision prismatic guides ensure continual accuracy and durability
each unit can be tilted by 2 degrees for a cleaner finish
Top and bottom trimming units (BC-5)
two high frequency sawing units running at 12,000 rpm trim the excess edging from the top and bottom of the panel
horizontal and vertical tracers with SIKO digital readouts for easy and precise adjustment
the two independent units can be tilted up to 20 degrees
each unit equipped with TC insert milling heads
roller type tracers work with high gloss and 3D effect panels and edges
Optional working units are available on the PRO 6 to PRO 13 models including;
Pre-milling unit (PF-12)
two high frequency milling units with pneumatic pressure control clean the panel edge prior to the edging application for optimum finish
Corner rounding unit (CR-1)
equipped with tracer with 3D sdjustment
programmable to 3 modes of corner rounding; square, rounded, bull nose
Grooving station (RN2.2)
to make a longitudinal groove on the upper face if the panel
powered by a high frequency motor with independent tracer
Radius scraper (RB-8)
to remove excess glue from the radius of the PVC/BC edging after top and bottom trimming
roller type horizontal and vertical tracers with SIKO digital readouts for quick and precise adjustment
air cleaning to tracers
Glue scraper unit (RR-8)
removes residual glue from the top and bottom of panel surface
two separate blade holders with independently adjustable copying devices
air cleaning to tracers
Buffing unit (PC-5)
restores the PVC/ ABS edge colour and polishes it after the trimming and scraping operations
two independent units with tilting motors running at 1500 rpm power the 100mm diameter cotton buffers
Cehisa UK
DaltonsWadkin
DaltonsWadkin
The CEHISA Pro Concept is a hot melt automatic through-feed edgebander suitable for melamine, PVC, ABS, PP and veneer edging up to a thickness of 3mm and solid edging up to 8mm. An intuitive 5.6″ or 10″ touch screen control gives the operator quick access for monitoring all machine functions – start/ stop, program editing, parameters check and editing, alarm diagnostics etc all in real time.
Panels are fed through the machine with an industrial chain-track system running on ground steel guides. Non-marking traction pads ensure a positive feed without damaging the panel surface while the synchronised top pressure beam with two sets of rollers keeps the panel secured against the track.
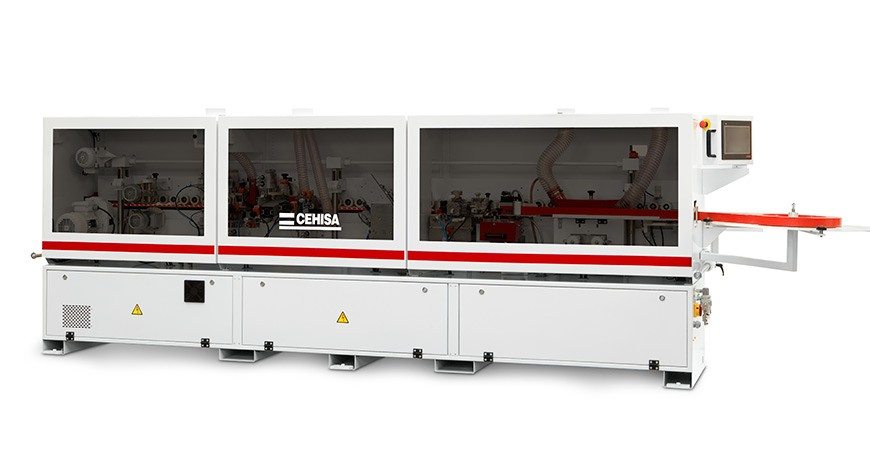
As standard the eight models within the PRO Concept range all include the following;
Feeding unit
roll tray for edging
feed up to 8mm thick solid edging manually
precision timed automatic edging feed minimising wastage
pneumatic cut-off guillotine
optional automatic magazine feeder for solid edging
Glue application unit (M-2NS)
new design with improved thermodynamics for quicker heating
quick change system for swapping the unit over in less than 60 seconds
full TEFLON coating
molten glue injected at the upper and lower points of the application roller where inbuilt heating elements maintain optimum application temperature
automatic temperature control by electronic thermostat to prevent scorching of glue while machine idle
1.5 kg glue tank capacity of solid aluminium casting machine to a smooth finish to allow uninterrupted glue flow
optional DUMELT system for use of both EVA and PUR adhesives
Pressure rollers
three rollers exert pressure to the edging against the panel to achieve adhesion
first roller is driven, the second and third are idle
the first roller is cylindrical and the second two conical in opposing positive and negative directions
SIKO digital readout for unit adjustment to 3mm edge/ 8mm solid edge
End trimming units (V-7)
two independent high frequency sawing units running at 12,000 rpm trim the ends of the edging flush to the panel
precision prismatic guides ensure continual accuracy and durability
each unit can be tilted by 2 degrees for a cleaner finish
Top and bottom trimming units (BC-5)
two high frequency sawing units running at 12,000 rpm trim the excess edging from the top and bottom of the panel
horizontal and vertical tracers with SIKO digital readouts for easy and precise adjustment
the two independent units can be tilted up to 20 degrees
each unit equipped with TC insert milling heads
roller type tracers work with high gloss and 3D effect panels and edges
Optional working units are available on the PRO 6 to PRO 13 models including;
Pre-milling unit (PF-12)
two high frequency milling units with pneumatic pressure control clean the panel edge prior to the edging application for optimum finish
Corner rounding unit (CR-1)
equipped with tracer with 3D sdjustment
programmable to 3 modes of corner rounding; square, rounded, bull nose
Grooving station (RN2.2)
to make a longitudinal groove on the upper face if the panel
powered by a high frequency motor with independent tracer
Radius scraper (RB-8)
to remove excess glue from the radius of the PVC/BC edging after top and bottom trimming
roller type horizontal and vertical tracers with SIKO digital readouts for quick and precise adjustment
air cleaning to tracers
Glue scraper unit (RR-8)
removes residual glue from the top and bottom of panel surface
two separate blade holders with independently adjustable copying devices
air cleaning to tracers
Buffing unit (PC-5)
restores the PVC/ ABS edge colour and polishes it after the trimming and scraping operations
two independent units with tilting motors running at 1500 rpm power the 100mm diameter cotton buffers
Cehisa UK
DaltonsWadkin